|
|
|
Mass finishing and sand blast machines and media
| |
|
Circular vibratory finishing macnine
Circular Vibratory Finishing Machines are specially designed for processing of all types of components, from high gloss polishing to heave deburring, radiusing, chamfering, grinding, descaling, degreasing, washing...
- Compact design.
- High abrasive efficiency, good surface finishing result.
- Heavy-duty electric vibration motor.
- Adjustable vibration control.
- High durable hot-poured polyu
PLZG/PLZGC (with cured wall) without integrated screening system, features flat-bottom, for processing a wide range of components from small, middle, delicate parts to large marble slabs, which easy damaged by dam and separation screen, or for a variety of parts of different sizes and batches, where automatic unloading does not have any particular advantage.
Option:
- Variable frequency drive speed controller control for automatic operation.
- Sound-proof lid to reduce the noise
- Compound metering system and flow meter
- Magnetic separator
PLZG |
Model |
Capacity (L) |
Power (kW) |
Dimensions LxWxH (mm) |
Weight (kg) |
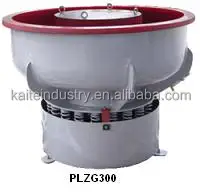 |
PLZG25 |
25 |
0.5 |
600 x 600 x 800 |
85 |
PLZG50 |
50 |
1.1 |
760 x 760 x 900 |
110 |
PLZG80 |
80 |
1.1 |
760 x 760 x 900 |
100 |
PLZG100 |
100 |
1.5 |
1050x1050x950 |
285 |
*PLZG100Z |
100 |
2.2 |
1050x1050x950 |
285 |
PLZG200 |
220 |
3 |
1200x1200x1000 |
400 |
PLZG300 |
260 |
3.7 |
1320x1320x930 |
600 |
*PLZG300Z |
260 |
5 |
1320x1320x930 |
600 |
PLZG400 |
400 |
5 |
1450x1450x1030 |
730 |
PLZG480 |
480 |
5 |
1430x1430x1100 |
730 |
PLZG600 |
660 |
5.5 |
1800x1800x1220 |
1300 |
*PLZG600Z |
660 |
7.5 |
1800x1800x1220 |
1300 |
PLZG800 |
780 |
7 |
1800x1800x1220 |
1300 |
PLZG900 |
900 |
7 |
1900x1900x1450 |
2200 |
PLZG1200 |
1200 |
11 |
2120x2120x1500 |
2200 |
PLZG1500 |
1500 |
14 |
2120x2120x1550 |
2400 |
PLZG2500 |
2500 |
18.5 |
2320x2320x1570 |
3000 |
PLZGC |
Model |
Capacity (L) |
Power (kW) |
Dimensions L x W x H (mm) |
Weight (KG) |
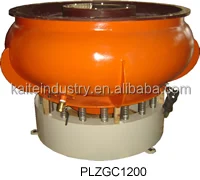 |
PLZGC30 |
30 |
0.5 |
600 x 600 x 810 |
100 |
PLZGC80 |
80 |
1.1 |
760 x 760 x 920 |
100 |
PLZGC100 |
100 |
1.5 |
1100x1100x950 |
285 |
*PLZGC100Z |
100 |
2.2 |
1100x1100x950 |
285 |
PLZGC200 |
200 |
3 |
1200x1200x1050 |
560 |
PLZGC300 |
300 |
3.7 |
1200x1200x1000 |
560 |
PLZGC300Z |
300 |
5 |
1200x1200x1000 |
560 |
PLZGC350 |
345 |
5 |
1450x1450x1030 |
600 |
PLZGC600 |
600 |
5.5 |
1800x1800x1220 |
1080 |
PLZGC600Z |
600 |
7.5 |
1800x1800x1220 |
1080 |
PLZGC900 |
900 |
9 |
1900x1900x1450 |
1800 |
PLZGC900Z |
900 |
11 |
1900x1900x1450 |
1800 |
PLZGC1200 |
1200 |
11 |
2120x2120x1500 |
2400 |
PLZGC1200Z |
1200 |
15 |
2120x2120x1500 |
2400 |
* |
suitable for steel ball burnishing |
Circular Vibratory Finishing Machines with an integrated screening system
LZG/LZGC (with cured wall,LZGS with straight wall) with an integrated screening system consisting of manually (standard option) or pneumatically activated separation flap and a built-in separation screen.Separating screen is changeable. Manually (standard option) or pneumatically activated separate flap for automatic separation, media and components are delivered over the separation screen and the media returns through the screen to the bowl and components discharge to a collect bin or secondary operation. This series machines are suited for the processing of high production, small components, or flat, lightweight parts which easy stick together. They are also suitable for steel ball burnishing processing.
Option: • Variable frequency drive speed controller control for automatic operation.
• Pneumatic operated separation flap for automatic operation. • Sound-proof lid to reduce the noise • Compound metering system and flowmeter • In-feed chute (only for LZGS series) for connection with other machinery for automatic processing line.
• Magnetic separator
LZGS |
Model |
Capacity (L) |
PU (mm) |
Power (KW) |
Dimensions LxWxH (mm) |
Weight (KG) |
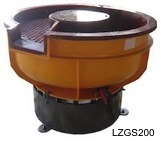 |
LZGS100 |
100 |
20 |
1.5 |
1300x1150x860 |
340 |
*LZGS100Z |
100 |
20 |
2.2 |
1300x1150x860 |
340 |
LZGS150 |
150 |
20 |
2.2 |
1250x1200x1020 |
360 |
LZGS200 |
200 |
20 |
3.0 |
1200x1200x1100 |
650 |
LZGS300 |
270 |
22 |
3.7 |
1400x1350x1000 |
650 |
*LZGS300Z |
270 |
22 |
5.0 |
1400x1350x1000 |
650 |
LZGS400 |
480 |
24 |
5.0 |
1480x1430x1100 |
780 |
LZGS600 |
660 |
26 |
5.5 |
2000x1800x1350 |
1400 |
*LZGS600Z |
660 |
26 |
7.5 |
2000x1800x1350 |
1400 |
LZGS900 |
900
|
26
|
9.0
|
2160x2153x1100
|
2200
|
* |
suitable for steel ball burnishing |
|
LZGC |
Model |
Capacity (L) |
PU (mm) |
Power (KW) |
Dimensions LxWxH (mm) |
Weight (KG) |
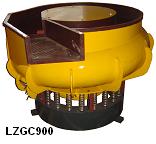 |
LZGC100 |
100 |
20 |
1.5 |
1170x1100x950 |
320 |
*LZGC100Z |
100 |
20 |
2.2 |
1170x1100x950 |
320 |
LZGC200 |
200 |
20 |
3.0 |
1310x1150x950 |
400 |
LZGC300 |
260 |
22 |
3.7 |
1480x1330x1050 |
650 |
*LZGC300Z |
260 |
22 |
5.0 |
1480x1330x1050 |
650 |
LZGC600 |
580 |
26 |
5.5 |
2000x1800x1350 |
1400 |
*LZCC600Z |
580 |
26 |
7.5 |
2000x1800x1350 |
1400 |
LZGC900 |
900 |
26 |
9.0 |
2200x2300x1550 |
2470 |
* |
suitable for steel ball burnishing |
|
|
Options:
- Variable frequency drive speed controller control for automatic operation.
- In-feed chute (only for LZGS series) for connection with other machinery for automatic processing line.
- Pneumatic operated separation flap for automatic operation.
- Sound-proof lid to reduce the noise
- Compound metering system
|
Tub vibratory finishing machines is suitable for processing medium and large sized delicate components with complex profile for deburring, chamferring, polishing, cleaning, burnishing, brightening, smoothing all kinds of metal, plastic and ceramic parts.
Tub vibratory finishing machine is also widely used for process marble stone to achieve antique appearance.
Feature
1. Driven by two vibratory motors, one each at the end of tub.
2. Tub can be divided into separate processing chambers by PU coated dividers to process delicate components to prevent part-on-part impact.
Options:
- VFD speed controller.
- Separate divider sheets.
- Compound pump and water flowmeter.
- Sound-proof lid.
XZG |
Capacity L |
Tub Inter Dimension L x W x H (mm) |
PU mm |
Power kw |
Overall Dimension L x W xH (mm) |
Weight kg |
XZG15* |
15 |
440 x 208 x 215 |
10 |
0.37 |
526 x 380x 555 |
85 |
XZG100 |
100 |
664 x 400 x 460 |
20 |
2 x 1.1 |
1320 x 615 x 860 |
350 |
XZG500 |
500 |
1310 x 690 x 700 |
25 |
2 x 2.2 |
2670 x 1000 x 985 |
700 |
XZG900 |
900 |
1200 x 900 x 850 |
25 |
2 x 4.0 |
2700 x 1050 x 1100 |
900 |
XZG1000 |
1000 |
2200 x 730 x 645 |
25 |
2 x 4.0 |
3662 x 970 x 1080 |
1600 |
XZG1200 |
1200 |
2000 x 750 x 854 |
25 |
2 x 4.0 |
3000 x 1050 x 1100 |
2100 |
XZG1800 |
1800 |
2020 x 1120 x 940 |
25 |
2 x 5.5 |
3500 x 1336 x 1256 |
2800 |
XZG2800 |
2800 |
1580 x 1510 x 1270 |
25 |
2 x 9.0 |
3300 x 1830 x 1740 |
4000 |
XZGC |
Capacity L |
Tub Inter Dimension L x D/W **x H (mm) |
PU mm |
Power kW |
Overall Dimension L x W xH (mm) |
Weight kg |
XZG240C** |
240 |
690 x 670/524 x 625 |
16 |
2 x 1.1 |
1880 x 880 x 920 |
450 |
XZG500C** |
500 |
1310 x670/ 524 x 625 |
16 |
2 x 2.2 |
2870 x 880 x 920 |
700 |
XZG750C** |
750 |
2000 x/670/ 524 x 625 |
16 |
2 x 2.2 |
3354 x 880 x 920 |
800 |
Remark |
* one motor only ** Processing tub with curved well. *** D=tub diameter, W=top open wide |
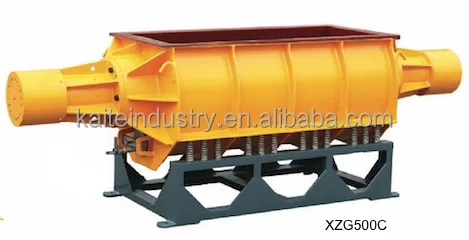 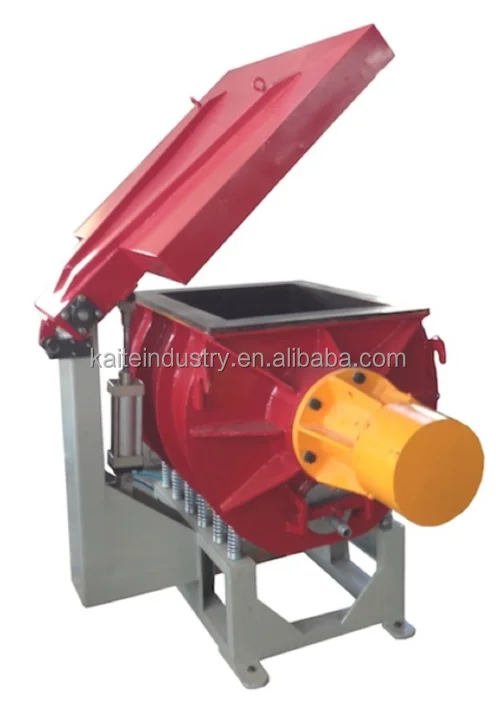 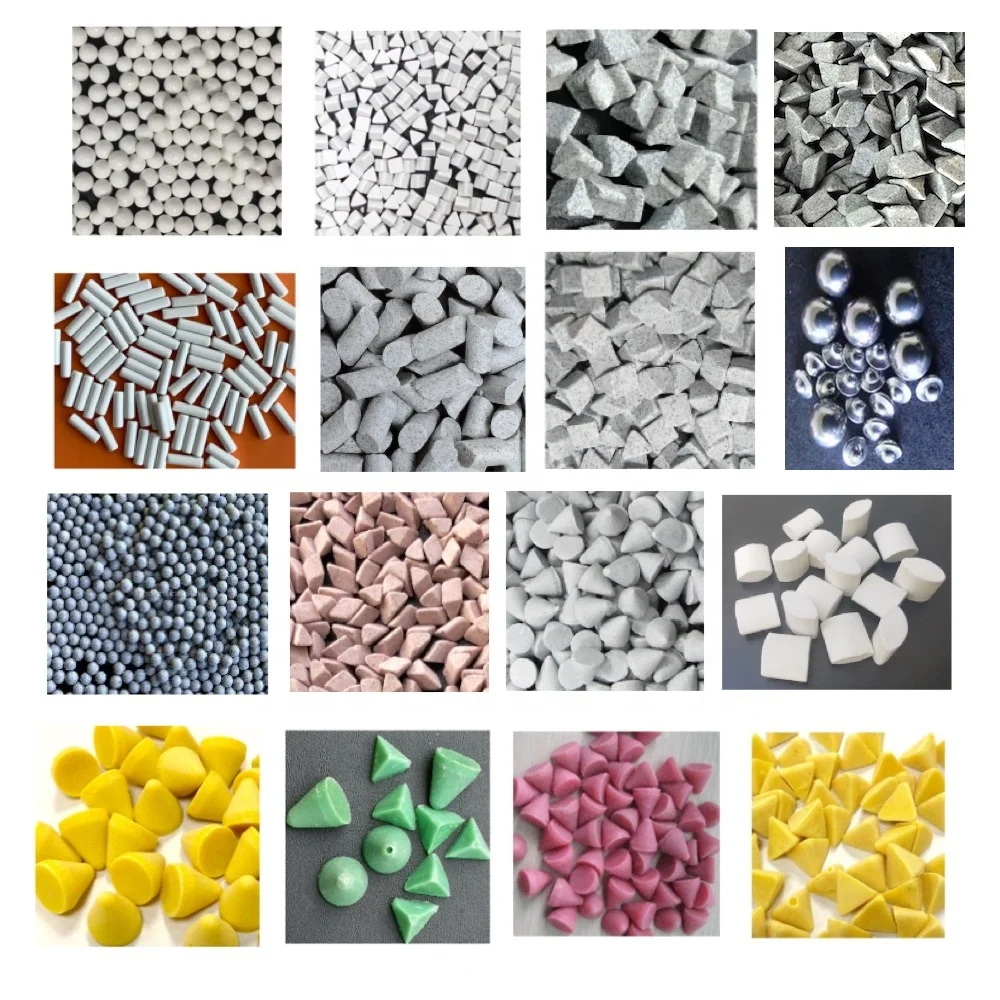
Centrifugal barrel finishing machines can be widely used to process various metal, plastic and ceramic componets, which have been formed by pressing, cutting, forging and heat treatment, for deburring, removing oxide and polishing. It is especially a kind of ideal polishing equipment for the complicated and irregular parts and the thin sheet parts that are easy to deform.
|
Feature:
- Finishing cycles up to 30 times faster over vibratory and rotary finishing.
- Consistent, repeatable process finishing
|
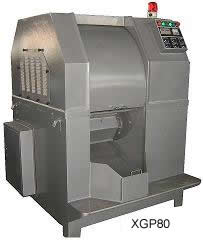 |
Model
|
Capacity (L)
|
Dimension / L x W x H (mm)
|
Weight (Kg)
|
Power (KW)
|
XGP16*
|
16 |
1260 x 900 x 1270 |
500 |
3.0 |
|
30
|
930 x 1042 x 1155
|
485
|
2.2
|
|
36
|
1130 x 930 x 1440
|
530
|
2.2
|
|
40
|
1300 x 1062 x 1400
|
600
|
4.0
|
|
60
|
1300 x 1130 x 1620
|
850
|
4.0
|
|
80
|
1375 x 1750 x 1562
|
800
|
5.5
|
|
120
|
1410 x 1450 x 1815
|
1300
|
5.5
|
|
140
|
1528 x 1750 x 1965
|
1500
|
7.5
|
|
160
|
1537 x 1770 x 2000
|
1650
|
7.5
|
|
200
|
1900 x 1810 x 2210
|
1870
|
11.0
|
|
320
|
2040 x 2200 x 2400
|
3100
|
15.0
|
Remark |
* vertical barrels ** XGP30, barres to be removable for loading/unloading *** 32 small barrel, 0.8L each small barrel |
Optional |
1. hexagon barrel
2. round barrel
3. skew axis
4. vibratory separator
5. compartment barrel to eliminate part on part impact
|
|
|
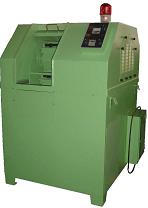 |
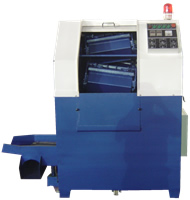 |
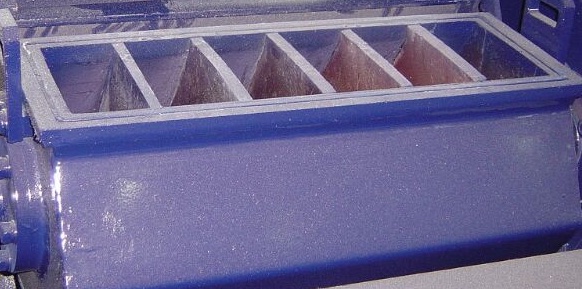 |
compatment barrel |
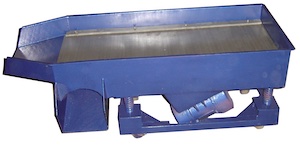 |
XGP30 |
XGP60X with vibratory seperator |
Vibratory separator |
|
Centrifugal Disc Finishing Machines |
Centrifugal Disc Finishing Machines are suitable for deburring,chamferring, polishing all kinds of metal, plastic and ceramic workparts in small to medium size at high speed. Centrifugal Disc Finishing Machines are ideal finishing machine especially for complexed profile and lamella proteiform parts. High speed processing allows for finishing performance upto 10 times faster than vibratory machine and over 20 times than barrel machine. The speed of spining disc can be regulated steplessly.Low noise, movement smoothly and stably.The working barrel lined Polyurethane inside for protracting working life.
Zero-gap Dry/Wet Disc Finishing Machine |
Zero-gap Dry/Wet Disc Finishing Machine has zero-gap between disc and barrel for processing very thin parts unto 0.1mm. Feature:
- Compact design suit for both wet and dry processing
- Working barrel is lined inside with hot poured high wear-resistant polyurethane for protracting working life.
- Tough bearing with high wear-resistant ceramic/tungsten ring for dry processing, PU/ceramic ring for wet processing.
- Zero gap for processing very thin parts unto 0.1mm.
- Variable frequency inverter Speed control for more option processing.
- Rotary in both clockwise and anti-clockwise.
PLC control with touch screen display for easy setting, operating and storage of all processing parameter |
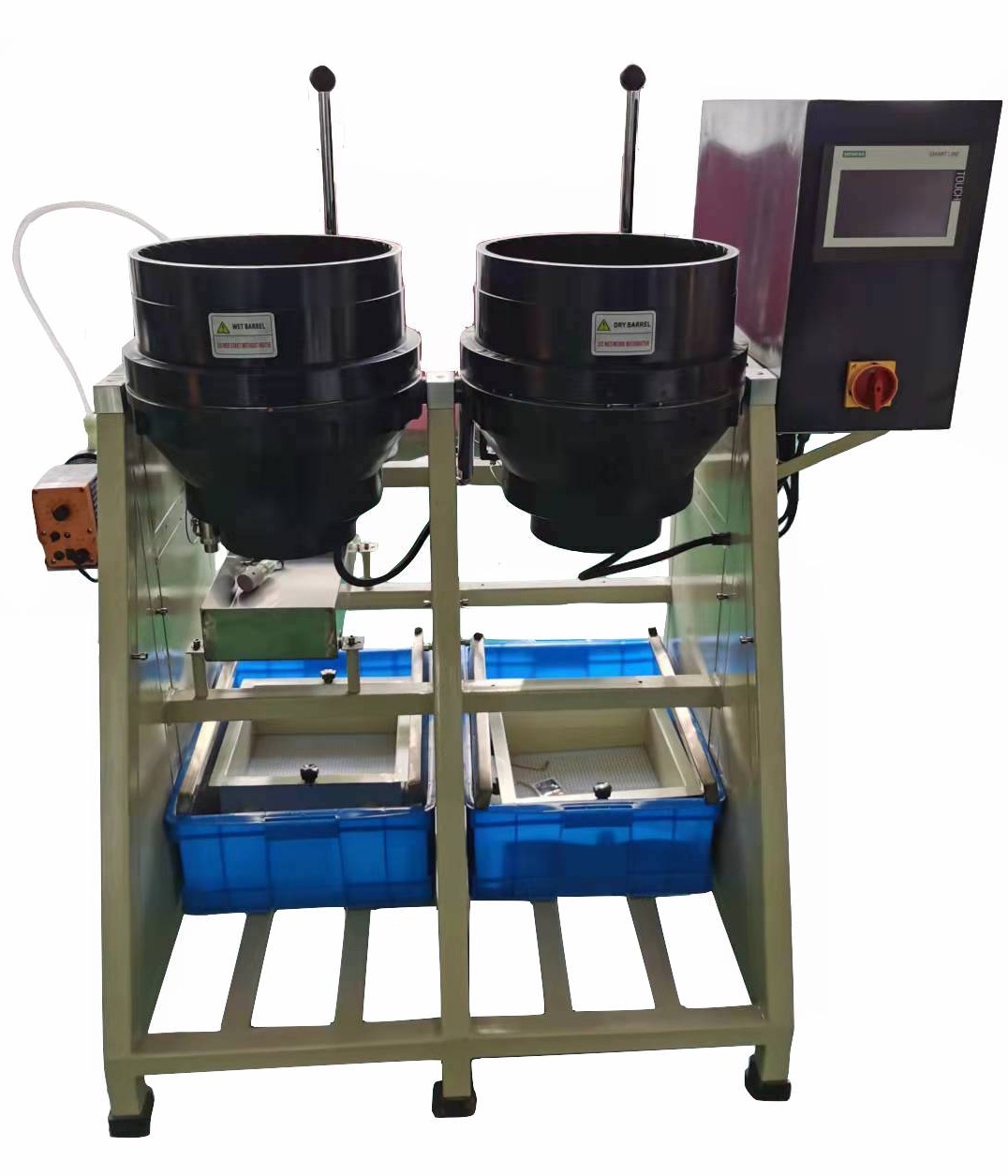 |
Model |
Capacity (L) |
Working capacity (L) |
Motor (kw) |
Speed Max. (rpm) |
Size (mm) |
Weight (kg) |
ZCF20 |
20 |
14 |
0.75 |
450 |
720x800x1450 |
140 |
ZCF20/2 |
2x20 |
2x14 |
2x0.75 |
450 |
1200x800x1450 |
245 |
ZCF50 |
50 |
40 |
2.2 |
380 |
1020x860x1600 |
215 |
ZCF50/2 |
2x50 |
2x40 |
2x2.2 |
380 |
1500x860x1600 |
360 |
|
|
 |
Precision Dry/Wet Centrifugal Disc Finishing Machine |
Precision Dry/Wet Centrifugal Disc Finishing Machine has fine gap 0.1-0.2mm between disc and barrel for processing thin workpieces. Feature:
- Compact design suit for both wet and dry processing
- Working barrel is lined inside with hot poured high wear-resistant polyurethane for protracting working life.
- Tough bearing with high wear-resistant ceramic/tungsten ring for dry processing, PU/ceramic ring for wet processing.
- Distinctive gap adjusting system
- Variable frequency inverter Speed control for more option processing.
- Rotary in both clockwise and anti-clockwise.
- Timer for repeatable precision processing.
|
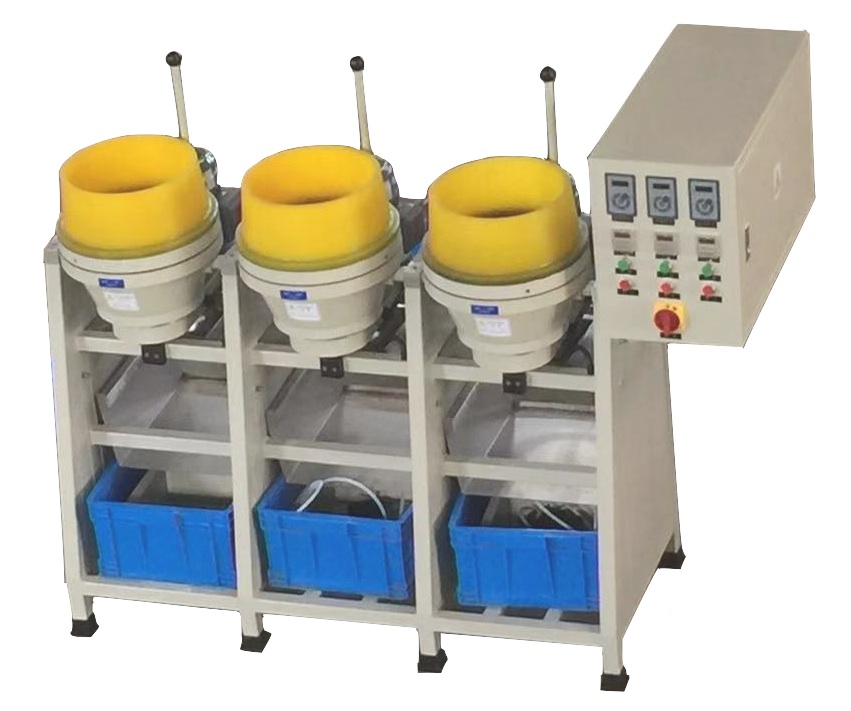 |
Model |
Capacity (L) |
Motor (kw) |
Speed max. (rpm) |
Size (mm) |
Weight (kg) |
PVA10 |
10 |
0.37 |
450 |
630*700*1250 |
70 |
PVA10/2 |
10x2 |
2x0.37 |
450 |
1030*700*1250 |
130 |
PVA10/3 |
10x3 |
3x0.37 |
459 |
1520*700*1250 |
190 |
PVA20 |
20 |
0.75 |
450 |
720x800x1450 |
140 |
PVA20/2 |
20x2 |
2x0.75 |
450 |
1180x800x1450 |
235 |
PVA20/3 |
20x3 |
3x0.75 |
450 |
1700x800x1450 |
330 |
PVA38 |
38 |
2.2 |
400 |
900x820x1450 |
220 |
PVA38/2 |
38x2 |
2x2.20 |
400 |
1500x820x1450 |
370 |
PVA38/3 |
38x3 |
3x2.20 |
400 |
2150x820x1450 |
530 |
|
|
 |
Manual Centrifugal Disc Finishing Machine |
LLB50, LLF50 and LLF120, the working barrel can be manually pivoted 100° for easy discharging of medias and parts.
Model
|
LLB10 |
LLB20 |
LLB50
|
LLF50
|
LLF120
|
LLD230
|
Barrel capacity (L)
|
11 |
24 |
50
|
50
|
120
|
230
|
Working capacity (L)
|
6 |
12 |
25
|
25
|
60
|
130
|
Motor power (KW)
|
0.75 |
1.1 |
1.5
|
1.5
|
4.0
|
7.5
|
Motor speed (RPM)
|
1500 |
1500 |
1500
|
125-1250
|
125-1250
|
940
|
Spiner disc speed (RPM)
|
0-350 |
0-250 |
50-180
|
50-180
|
50-160
|
0-140
|
Discharge height (mm)
|
500 |
400 |
280
|
280
|
320
|
550
|
Dimensions (mm)
|
L |
730 |
1020 |
1000
|
1390
|
1740
|
1620
|
W |
630 |
800 |
660
|
700
|
900
|
1008
|
H |
1060 |
1360 |
1120
|
1240
|
1470
|
1135
|
Noise (dB)
|
≤60 |
≤60 |
≤60
|
≤60
|
≤60
|
≤80
|
Weight (Kg)
|
200 |
300 |
300
|
400
|
600
|
1100
|
|
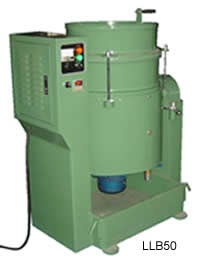 |
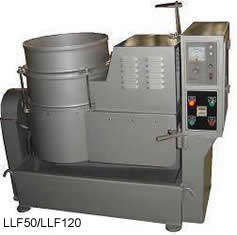 |
.jpg) |
|
|
 |
Semi-auto Centrifugal Disc Finishing Machine |
|
LLF120M and LDG240M fitted with motor drivn pivoting system for automatically discharging mixture of parts and media and vibratory separatot for automaically separating media from parts. |
Model
|
LLF120M
|
Barrel capacity
|
120 L
|
Working capacity
|
60 L
|
Spiner motor
|
Power |
4.0 kw
|
Speed |
960 rpm
|
Spiner disc speed
|
0-160 rpm
|
Vibratory motor |
Power |
2 x 0.25kw |
Speed |
1450 rpm |
Pivot motor |
Power |
0.75 kw |
Speed |
910 rpm |
Barrel pivoting
|
150 degree |
Discharge height |
Meida |
380 mm
|
Parts |
250 mm |
Dimensions
|
1700 x 1380 x 1410 mm
|
Weight
|
1100 kg
|
Operation noise (dB) max
|
≤80
|
|
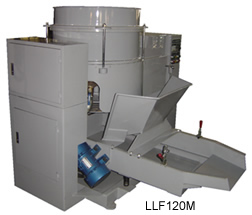 |
|
|
|
|
|
 |
Automatic Centrifugal Disc Finishing Machine |
|
LLF120A automatic centrifugal dics finishing machine, fitted with hydraulic loading system for automatically feeding media and parts into the working barrel, hydraulic pivoting system for automatically discharging the mixture of media and parts into intermediate hopper, vibratory separating system for separating media from parts, classifing undersiaed media, return the the reusable media to loader and discharging parts automatically..
|
Model
|
LLF120A
|
Barrel capacity
|
120 L
|
Working capacity
|
60 L
|
Spiner motor
|
Power |
5.5 kw
|
Speed |
1440 rpm
|
Spiner disc speed
|
0-160 rpm
|
Pivot/loader motor |
Power |
1.1 kw |
Speed |
910 rpm |
Vibratory motor |
Power |
2 x 0.12kw |
Speed |
1450 rpm |
Barrel pivoting
|
140 degree
|
Dimensions
|
2060 x 1700 x 1200mm
|
Weight
|
1200 kg
|
|
.jpg) |
|
|
LLF230x2 Automatic double batch centrifugal dics finishing machines combinate two automatic disc finishing machine by sharing one intermediate hopper and one screening machine only. While one batch with finished parts is separated on the screening machine, a second batch is processed in the work bowl, save idle times for parts/media separation.
|
Model |
LLF230x2 |
Capacity |
230L x 2 |
PU thickness |
12mm |
Spiner motor Power |
11kw x 2, 960rpm |
Spiner Speed |
0-140 rpm |
Hydraulic power |
21MPa. Pump 3kw, 1430rpm |
Separator system |
1.12kw |
Loading |
200L x 2 |
Compound dosing |
0.7Mpa , 13L/hx2 |
Water dosing |
0.7Mpa , 240L/h |
Weight |
4000kg |
Dimension |
L |
4500 mm |
W |
3375 mm |
D |
1780 mm |
|
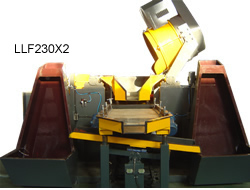 |
|
 |
|
|
|
|
|
Rotary Finishing Machine |
Rotary Finishing Machines are used for polishing small sizes componets, standardized parts and components, and all kinds of componets which are made of ferrous metal, nonferrous metal and nonmetal. It can improve the surface quality of the componets efficiently, and can be widely applied to polish a large quantity of spare parts. This type of machines have a simple but strong structure, safe for use. It is also equipped with a timer, so that one can operate several machines at one time.
Equipped with reduction device for smooth running. Inverter variable speed control for more processing options. Hot poured, high wear-resistant polyurethane lined barrel has longer working life. The barrel jog button make the barrel to be positioned propely for easy loading/unloading. |
|
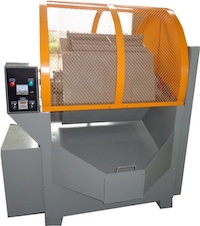 |
Single barrel rotary finishing machines |
Model
|
Capacity
(L)
|
PU thickness (mm) |
Barrel speed (r/min)
|
Power
(KW)
|
Dimension
L x W x H (mm)
|
Weight
(Kg)
|
WGP50
|
50
|
10 |
60
|
1.0
|
730 x 720 x 1200
|
150
|
WGP100
|
100
|
10 |
40
|
1.1
|
1020 x 900 x 1300
|
200
|
WGP200
|
200
|
10 |
30
|
2.2
|
1090 x 1000 x 1420
|
500
|
WGP300
|
300
|
10 |
30
|
2.2
|
1450 x 1000 x 1420
|
560
|
WGP500
|
500
|
10 |
25
|
5.5
|
1660 x 1300 x 1520
|
1000
|
|
|
Double barrel rotary finishing machines |
Model
|
Capacity
(L)
|
Barrel Speed (r/min)
|
Dimension
L x W x H (mm)
|
Weight
(Kg)
|
Power
(KW)
|
WGP2x140
|
2x140
|
40
|
2570×850×1267
|
100
|
3
|
WGP2x300
|
2x300
|
30
|
3000×1300×1450
|
560
|
4
|
WGP2x500
|
2x500
|
25
|
3870×1150×1420
|
1000
|
7.5
|
|
|
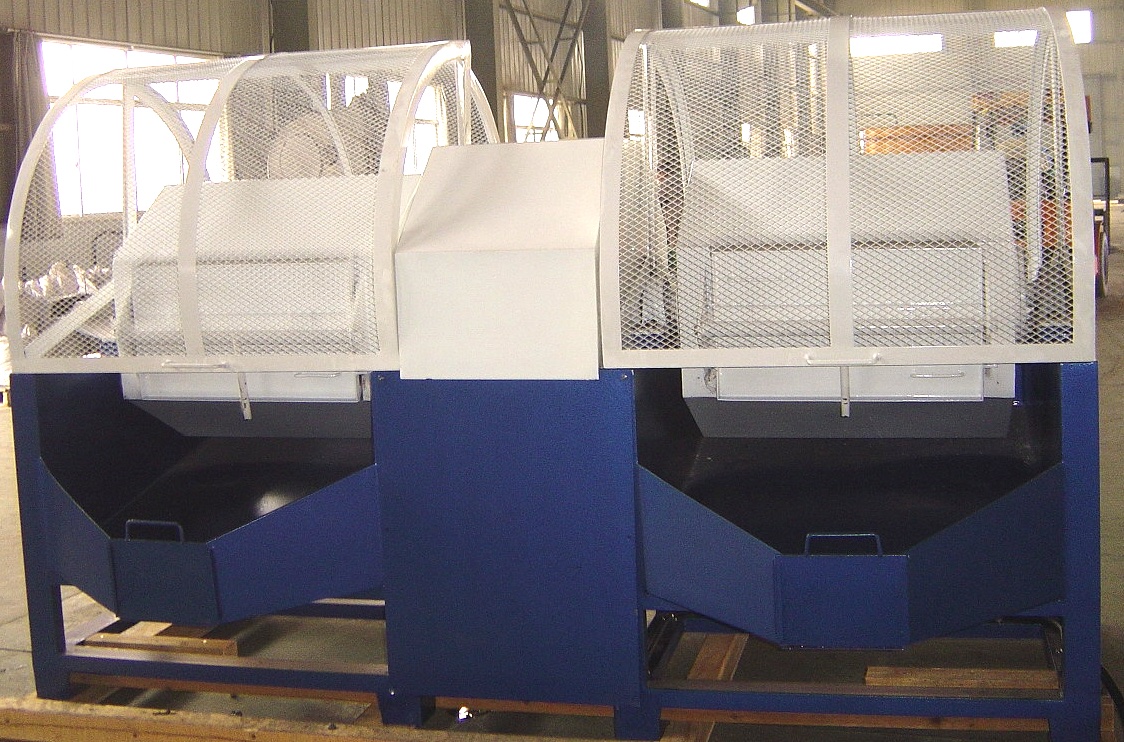 |
Ceramic Media and Porcelain Media
Ceramic Media are made of high quality of abrasives, such as brown fused alumina, white fused alumina, pink fused alumina, black silicon carbide, green silicon carbide, alumina, etc., vitrified bonded at high temperature. Ceramic medias are widely used in grinding, polishing, finishing of the surfaces of metal parts with irregular or regular surfaces for better finish, and also widely used for chamfering , deburring, scaling oxide, removing rusty stain as a mass-production method. Ceramic medias find wide applications in machinery , bearing , electronic, hard-metals, camera, watch, bicycle, sew-machine, jewelery as well as arts and crafts industries.
Ceramic media are available in heavy cutting, medium cutting and light cutting.
Porcelain media are made of alumina, which is mainly used for fine finishng and burnishing, can be available in white, yellow or green color.
Applications:
Automotive industry Aerospace industry Medical industry Surgical instruments Coin industry Jewelry industry Cutlery cleaning Hardware tools Stone industry Casting parts Forging parts Stampings Turn and Milled parts 3D printing
|
|
|
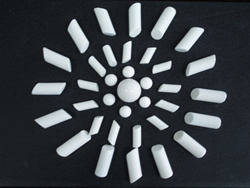 |
|
|
|
 |
Shape |
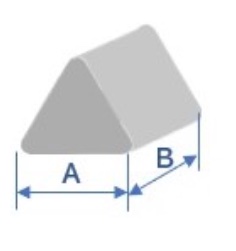 |
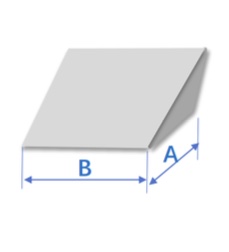 |
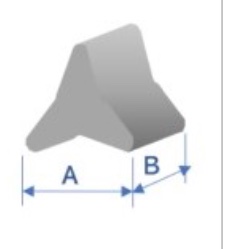 |
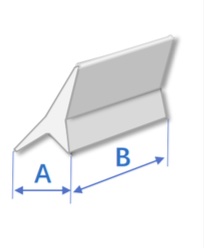 |
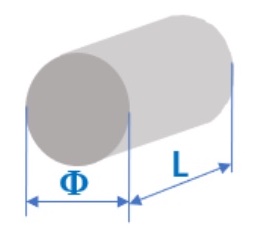 |
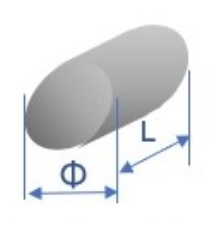 |
|
|
Triangle |
Angle-cut triangle |
Tristar |
Angle-cut tristar |
Cylinder |
Angle-cut cylinder |
Ball |
Grinding Perfomance |
A x B |
A x B |
A x B |
A x B |
¢ x L |
¢ x L |
¢ |
Very Heavy Grinding Heavy grinding Middle grinding Fine grinding Polishing |
2 x 2, 3 x 3, 3 x 6, 4 x 4, 4 x 6, 4 x 8, 5 x 5, 6 x 6, 8 x 8, 10 x 10, 12 x 12, 15 x 15, 18 x 18, 20 x 20, 25 x 25, 30 x 30, 30 x 40, 35 x 35, 40 x 40, |
3 x 3 3 x 6, 4 x 4, 4 x 6, 4 x 8, 5 x 5, 6 x 6, 8 x 8, 10 x 10, 12 x 12, 15 x 15, 18 x 18, 20 x 20, 25 x 25, 30 x 30, 30 x 40, 35 x 35, 40 x 40, |
4 x 4, 5 x 5, 5 x 10, 6 x 13, 7 x 5, 7 x 10, 10 x 6, 16 x 6, 16 x 16, 22 x 8, 22 x 10, 22 x 22, 28 x 10, 35 x 16 |
4 x 4, 5 x 5, 5 x 10, 6 x 13, 7 x 5, 7 x 10, 10 x 6, 16 x 6, 16 x 16, 22 x 8, 22 x 10, 22 x 22, 28 x 10, 35 x 16 |
2 x 5, 3 x 6, 4 x 6, 4 x 8, 5 x 10, 6 x12, 6 x 16, 7 x 13, 8 x 8, 8 x 16, 10 x 20, 12 x 12, 12 x 25, 14 x 20, 15 x 25, 15 x 30, 15 x 38, 20 x 20, 20 x 30, 22 x 22, 25 x 25, 25 x 35 40 x 40 |
2 x 5, 3 x 6, 4 x 6, 4 x 8, 5 x 10, 6 x12, 6 x 16, 7 x 13, 8 x 8, 8 x 16, 10 x 20, 12 x 12, 12 x 25, 14 x 20, 15 x 25, 15 x 30, 15 x 38, 20 x 20, 20 x 30, 22 x 22, 25 x 25, 25 x 35 40 x 40 |
1.0, 2.0, 3.0, 4.0, 5.0, 6.0, 8.0, 10.0, 12.0, 15.0, 18.0, 20.0, 22.0, 25.0, 30.0, 35.0 |
Shape |
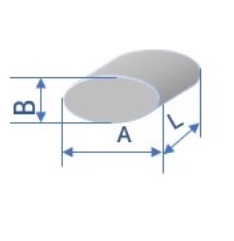 |
|
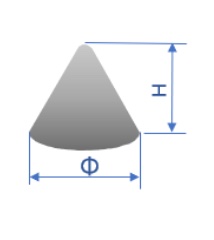 |
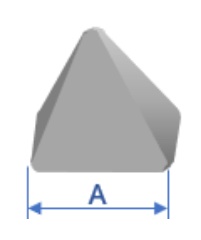 |
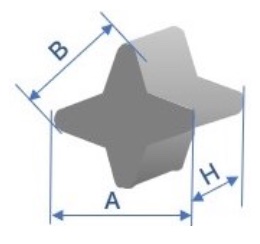 |
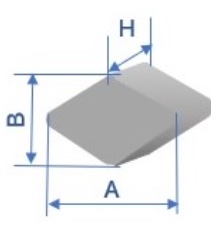 |
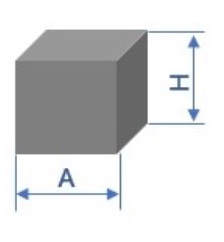 |
|
Ellipse |
Triangle-cut cylinder |
Cone |
Pyramid |
4-star |
Rhombus |
Cubic |
Grinding Perfomance |
A x B x L |
¢ x L |
¢ x H |
A |
A x B x H |
A x B x H |
A x H |
Very Heavy Grinding Heavy grinding Middle grinding Fine grinding Polishing |
8 x 3 x 8, 10 x 5 x 10, 15 x 7x 15, 20 x 10 x 20, 25 x 15 x 25, |
16 x 16, 12 x 12, 19 x 19, 25 x 25, 50 x 50 |
10 x 10, 15 x 15, 20 x 20, 25 x 25, 25 x 30, 30 x 30 35 x 38 |
10, 15, 20 |
45 x 32 x 15, 18 x 10 x 9.0, 35 x 17 x 11, |
15 x 10 x 10, 23 x 16 x 10, 26 x 25 x 18, 46 x 30 x 20 |
2 x 2, 4 x 4, 6 x 6, 8 x 8, 10 x 10, 15 x 15, 20 x 20 |
|
|
|
Porcelain Media |
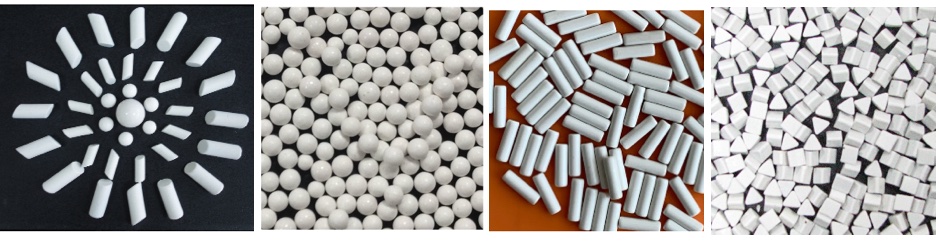 |
Shape |
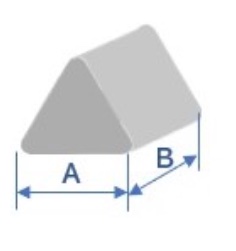 |
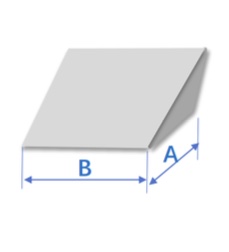 |
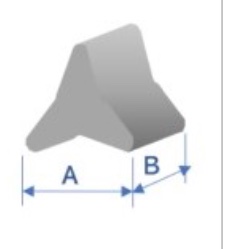 |
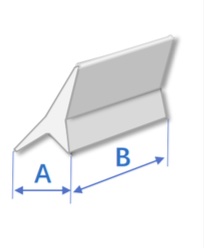 |
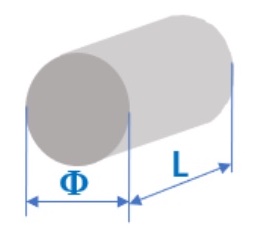 |
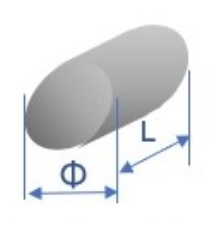 |
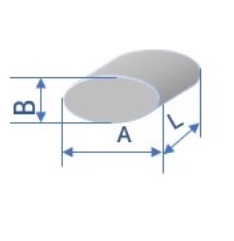 |
 |
|
Triangle |
Angle-cut triangle |
Tristar |
Angle-cut tristar |
Cylinder |
Angle-cut cylinder |
Ellipse |
Ball |
Density |
A x B |
A x B |
A x B |
A x B |
¢ x L |
¢ x L |
A x B x L |
¢ |
2.7g/cm3 |
2 x 2, 3 x 3, 3 x 6, 4 x 4, 4 x 6, 4 x 8, 5 x 5, 6 x 6, 8 x 8, 10 x 10, 12 x 12, 15 x 15, 17 x 17 |
2 x 2, 3 x 3, 3 x 6, 4 x 4, 4 x 6, 4 x 8, 5 x 5, 6 x 6, 8 x 8, 10 x 10, 12 x 12, 15 x 15, 17 x 17 |
4 x 4, 5 x 5, 5 x 10, 6 x 13, 7 x 5, 7 x 10, 10 x 6, 16 x 6, 16 x 16, 22 x 8, 22 x 10, 22 x 22, |
4 x 4, 5 x 5, 5 x 10, 6 x 13, 7 x 5, 7 x 10, 10 x 6, 16 x 6, 16 x 16, 22 x 8, 22 x 10, 22 x 22, |
1.5 x 3 2 x 5, 3 x 6, 4 x 6, 4 x 8, 5 x 10, 6 x12, 6 x 16, 7 x 13, 8 x 8, 8 x 16, 10 x 20, 12 x 12, 12 x 25, 15 x 15, |
1.5 x 3 2 x 5, 3 x 6, 4 x 6, 4 x 8, 4 x 14, 5 x 10, 6 x12, 6 x 16, 7 x 13, 8 x 8, 8 x 16, 10 x 20, 12 x 12, 12 x 25, 15 x 15 |
8 x 3 x 8, 10 x 5 x 10, 15 x 7x 15, 20 x 10 x 20, 25 x 15 x 25, |
1.0, 1.5, 2.0, 3.0, 4.0, 5.0, 6.0, 8.0, 10.0, 12.0, 15.0, 18.0, 20.0, 22.0, 25.0, |
3.2g/cm3 |
|
|
|
|
1.7 x 5.2, 2 x 7.5, 3 x 10, 3.5 x 10, 4.5 x 14 5 x 16 7 x 23 |
|
|
1.0, 1.5, 2.0, 3.0, 4.0, |
|
 |
Plastic Media |
Plastic Media are made of high quality of abrasives and plasic resin, generally used for gentle processing of almost all materials, but soft and lower bulk density nature makes it particalarly suitable for polishing of soft componentss like aluminium, zinc, copper, brass, glod and silver. Plastic media can provide high surface finish and widely used for pre-plate finishing.
|
Available grinding grades:
- Heavy
- Medium
- Light
- Super fine
Available colors:
- White,
- Brown,
- Blue,
- Yellow,
- Red.
- Blac
|
Cone |
Tetrahedron |
Pyramid |
Tristar |
Paraboloid |
Tristar pyramid |
|
 |
 |
 |
 |
 |
 |
|
a |
a |
a |
a x b |
a |
a |
Heavy grinding |
6 10 12 15 20 25 30 35 40 45 50 60 |
10 15 20 23 25 30 35 40 45 50 60 80 |
6 8 10 |
50x20 45x15 |
40 50 65 |
20 30 40 60 |
Middle grinding |
Fine polishing |
Super fine polishing |
|
|
|
|
|
Ceramic Beads |
Ceramic Beads have very fine microstructure featured strong mechanical resistance and high toughness, chemically inert, low-dust emission, do not contaminate the treated surface, especially suited for tool cleaning and surface preparation applications. |
Cearmic beads have Higher density than glass beads and thus a better treatement efficiency and Lower density than steel shot, which allows to save energy and preserve work parts. They're stable with high finishing efficiency and low abrasion to equipment.The treated surface of parts is smooth,uniform and even without contamination.They are widely used for gentle cleaning, descaling, deburring, smoothing, dulling, surface-finishing, hardening, shot peening etc. |
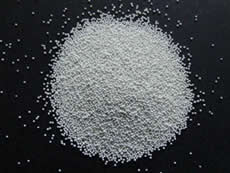 |
Physical & Chemical Index |
True Specific Gravity
|
3.86
|
Bulk Density
|
2.35 g/cm3
|
Compressive Strength
|
710N
|
Mohs Hardness
|
7.2
|
|
68%(+/-3%)
|
SiO
2
|
32%(+/-3%)
|
|
|
|
Available sizes for sand blasing |
|
Diameter (mm)
|
|
|
|
|
|
0.250--0.425
|
|
0.125--0.250
|
|
0.070--0.125
|
|
0--0.125
|
|
0--0.070
|
|
Available sizes for shot peening
|
Grit No.
|
Diameter (mm)
|
Z-850
|
0.850—1.180
|
Z-600
|
0.600—0.850
|
Z-425
|
0.425—0.600
|
Z-300
|
0.300--0.425
|
Z-210
|
0.210—0.300
|
Z-150
|
0.150—0.210
|
Z-100
|
0.100—0.150
|
|
|
Glass Beads for Sand Blasting |
Glass beads have perfect spheres with a smooth, brilliant surface, chemically inert, widely used in wet or dry method for prestressing shot peening, cleaning, trimming, surface finishing, smooth and deburring processing in industrial fields of aerospace, automotive, and electronics. |
Applications: Prestressing shot peening of gears, shafts, blades, cutting tools, pipes, joints and delicate parts, propellers and hulls, jet engine components blades, vanes, valves, spindles, shafts to increase the mechanical resistance to fatigue and stress corrosion cracking and work life of the parts. Surface finishing of metal, plastic, glass, wood, etc to produce a surface with finishing from fine matt to bright satin. Removing of debris from vats, tubes, trays, utensils, tanks, removing of old coating from surface. Cleaning of machinery, dies, plates, molds, pistons, blocks, large turbines and engine castings, intricate parts. Glass bead is chemical inert, so there is no surface contamination, post treatment for removal of contamination smears is unnecessary. |
|
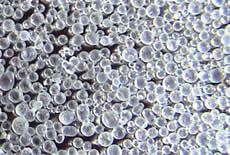 |
|
Chemical & Physical Properties |
Basic material
|
SiO
270% min
|
Shape
|
Spherical
|
Color
|
Clear
|
Specify gravity
|
2.4-2.6 |
Density |
1.5g/cc |
Hardness(Moh's)
|
5.5-6.0 |
Roundness |
80% min |
Free Si
|
0 |
|
|
Available sizes
|
400 - 800 micron |
|
90 - 150 micron |
300 - 400 micron |
|
70 - 110 micron |
200 - 300 micron |
|
55 - 100 micron |
150 - 200 micron |
|
40 - 70 micron |
100 - 200 micron |
|
0 - 50 micron |
Other sizes also can be available on request. |
|
|
Typical Chemical Contents
|
SiO2
|
72.60%
|
Na2O
|
13.40%
|
K2O
|
0.30%
|
Ca2O
|
8.02%
|
MgO
|
2.80%
|
Al2O3
|
0.75%
|
Free Si |
0 |
|
 |
|
 |
Garnet |
Almandine garnet is a natural abrasive in dark red color, made of garnet mineral rock. It is inert and non-toxic, environmental friendly material, has a very low dust emission,which make it an ideal abrsive media for sand blasting, sand cleaning, water jet cutting, it is also suitable for lapping, making organic bonded abrasive tools, glass polishing, and used as water filtration media, etc.
|
|
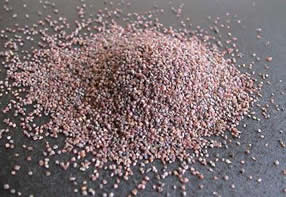 Typical applications: Lapping Making coated or bonded abrasive tools Sand blasting media Denim blasting Water filtration media Water jet-cutting abrasive Glass polishing High temperature gravel pack for deep oil wells. |
Chemical & Physical Typical Value
|
SiO2 |
39.12 % |
Al2O 3 |
20.92 % |
FeO |
23.89 % |
Fe2O3 |
4.15 % |
MnO |
0.15 % |
TiO2 |
0.095 % |
MgO |
9.78 % |
CaO |
9.56 % |
Free Si. |
0 % |
Cl- |
0.00 % |
Specify gravity |
3.97 |
Bulk Density (#80) |
2.15g/cm3 |
Hardness Moh's |
7.64 |
Melt point |
1340oC |
|
|
Available Grit
|
Grit No. |
Micron |
Grit No. |
Micron |
Grit No. |
Micron |
Grit No. |
Micron |
10/20 |
2000 ~ 850 |
30 |
710 ~ 600 |
54 |
355 ~ 300 |
90 |
180 ~ 150 |
20/40 |
850 ~ 425 |
36 |
600 ~ 500 |
60 |
300 ~ 250 |
100 |
150 ~ 125 |
30/60 |
600 ~ 250 |
40 |
500 ~ 425 |
70 |
250 ~ 212 |
120 |
125 ~ 106 |
24 |
850 ~ 710 |
46 |
425 ~ 355 |
80 |
212 ~ 180 |
150 |
106 ~ 75 |
Other sizes can be also available upon request.
|
|
 |
 |
|
Plastic Blasting Media (PBCM) is designed specifically for deflashing, coating removal, paint stripping, mold cleaning and surface preparation. Engineered for high performance, PBCM is clearly the leader when it comes to productivity and value. This is sometimes called Plastic Media, PMB (Plastic Media Blassting) or Plastic Abrasives.
They are 6 kinds of Plastic Blasting Media available: Melamine Formaldehyde, Urea Formaldehyde, Polycarbonate Cryogenic, Nylon Polyamide, Acrylic , Poly Allyl Di-Glycol Carbonate.
|
|
Melamine Formaldehyde Grit: MF 12-16, 16-20, 20-30, 30-40, 40-60 Application: a). used for deflashing discrete products and other components in electronics industries and die casting. b). for cleaning mold when it has stain in rubber product molding. c). for Paint Stripping. |
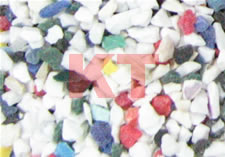 |
Type
|
Sieve No
|
Dimension(inch)
|
Dimension(mm)
|
MF 12 - 16
MF 16 - 20
MF 20 - 30
MF 30 - 40
MF 40 - 60
MF 60 - 80
|
12 / 16
16 / 12
20 / 30
30 / 40
40 / 60
60 / 80
|
0.066 / 0.047
0.047 / 0.033
0.033 / 0.023
0.023 / 0.016
0.016 / 0.010
0.010 / 0.007
|
1.70 / 1.18
1.18 / 0.85
0.85 / 0.60
0.60 / 0.42
0.42 / 0.25
0.25 / 0.18
|
|
|
|
Urea Formaldehyde Grit: UF12-16,16-20, 20-30, 30-40, 40-60 Application: a). used for deflashing discrete products and other components in electronics industries. b). for cleaning mold when it has stain in rubber product molding. c). for Paint Stripping. |
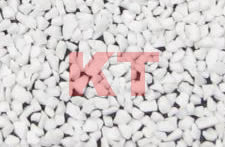 |
Type
|
Sieve No
|
Dimension(inch)
|
Dimension(mm)
|
UF 12 - 16
UF 16 - 20
UF 20 - 30
UF 30 - 40
UF 40 - 60
UF 60 - 80
|
12 / 16
16 / 12
20 / 30
30 / 40
40 / 60
60 / 80
|
0.066 / 0.047
0.047 / 0.033
0.033 / 0.023
0.023 / 0.016
0.016 / 0.010
0.010 / 0.007
|
1.70 / 1.18
1.18 / 0.85
0.85 / 0.60
0.60 / 0.42
0.42 / 0.25
0.25 / 0.18
|
|
|
|
Polycarbonate Cryogenic Grit: PCC20,30,38,45,60 Application: used for deflashing in rubber product molding, engineering plastic molding & die casting if they have cryogenic deflashing machine. |
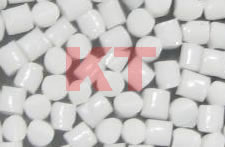 |
Type
|
Dimension(INCH)
|
dimension(mm)
|
L
|
D
|
L
|
D
|
PCC-80
PCC-60
PCC-45
PCC-38
PCC-30
PCC-20
PCC-15
|
0.080
0.060
0.045
0.038
0.030
0.020
0.015
|
0.080
0.060
0.045
0.038
0.030
0.020
0.015
|
2.00
1.50
1.14
1.00
0.75
0.50
0.38
|
2.00
1.50
1.14
1.00
0.75
0.50
0.38
|
|
|
|
Nylon-Red (Polyamide) Grit: NR-20,30,40,60,80 Application: used for ambient deflashing in engineering plastic molding. |
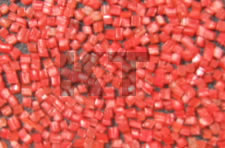 |
Type
|
Dimension(inch)
L x W x H
|
dimension(mm)
L x W x H
|
NR - 80
NR - 60
NR - 40
NR - 30
NR - 20
|
0.080 x .0.080 x .0.080
0.060 x .0.060 x .0.060
0.040 x .0.040 x .0.040
0.030 x .0.030 x .0.030
0.020 x .0.020 x .0.020
|
2.00 x 2.00 x 2.00
1.50 x 1.50 x 1.50
1.00 x 1.00 x 1.00
0.75 x 0.75 x 0.75
0.50 x 0.50 x 0.50
|
|
|
|
Acrylic |
Grit: AC 12-16,16-20, 20-30, 30-40, 40-60 Application: used for blast cleaning depending on product that requires blasting. |
Type
|
Sieve No
|
Dimension(inch)
|
Dimension(mm)
|
AC 12 - 16
AC 16 - 20
AC 20 - 30
AC 30 - 40
AC 40 - 60
AC 60 - 80
|
12 / 16
16 / 12
20 / 30
30 / 40
40 / 60
60 / 80
|
0.066 / 0.047
0.047 / 0.033
0.033 / 0.023
0.023 / 0.016
0.016 / 0.010
0.010 / 0.007
|
1.70 / 1.18
1.18 / 0.85
0.85 / 0.60
0.60 / 0.42
0.42 / 0.25
0.25 / 0.18
|
|
|
Poly Allyl Di-Glycol Carbonate |
Grit: PCG12-16,16-20, 20-30, 30-40, 40-60 Application: used for blast cleaning depending on product that requires blasting. |
Type
|
Sieve No.
|
Dimension(inch)
|
Dimension(mm)
|
PCG 12 - 16
PCG 16 - 20
PCG 20 - 30
PCG 30 - 40
PCG 40 - 60
PCG 60 - 80
|
12 / 16
16 / 12
20 / 30
30 / 40
40 / 60
60 / 80
|
0.066 / 0.047
0.047 / 0.033
0.033 / 0.023
0.023 / 0.016
0.016 / 0.010
0.010 / 0.007
|
1.70 / 1.18
1.18 / 0.85
0.85 / 0.60
0.60 / 0.42
0.42 / 0.25
0.25 / 0.18
|
|
 |
Wet Blast Cabinet |
Wet blast cabinets consist of Cabinet enclosure, exhauster, and polyurethane sand pump, can available with cabinet either reinforced fiberglass or 100% stainless steel. Cabinet enclose water and blasting environment to provide efficient blast cleaning while maintaining a clean surrounding work area. Wet blasting can be used for cleaning and finishing all kinds of parts, produce a smooth, a sericeous surface, a bright shine appearance. Compared to dry blast operation, wet blast does not produce static electricity, is also non-hazardous, dust-free and prevents hours of messy cleaning... |
Features: 1. Dust-free wetblasting reduces worker exposure to dust and static electricity build-up generated by dry blasting. 2. 24" long blast gloves wear resistane rubber and protect oprtator hands. 3. Staineless Steel cabinet or reinforced fiberglass cabinet provide rust-free blasting environment. 4. Safety interlocks interrupt blasting if either door is opened. 5. Sopylights brightly illuminates work chamber. 6. exhauster maximizes visibility nside cabinet. 7. Pneumatic powered Windscreen wipers maintains clean window for clear view of work. 8. Foot pedal activates blast process and minimizes operator fatigue. 9. Built-in fingertip-activated squirt gun rinsing the parts inside the working cabinet. 10. Pressure regulator, gauge, and electric switch mounted within easy reach. |
|
 |
|
|
|
|
9065W
|
|
|
|
|
|
|
|
|
|
|
|
|
Door opening, mm |
650 x340
(front-top)
|
470x610
(side)
|
570x630
(side)
|
950x950
(side)
|
View Window, mm |
650x340
|
570x230
|
570x230
|
570x230
|
Light |
18W
|
18W x 2
|
18W x 2
|
18w x 2
|
|
|
1.1KW
|
1.1KW
|
1.1KW
|
Exhauster Fan |
38W
|
38W x 2
|
38W x 2
|
38W x 2
|
Media tank |
water |
20kg
|
25kg
|
30kg
|
60kg
|
media |
4kg
|
5kg
|
6kg
|
10kg
|
|
|
reinforced fiberglass or stainless steel |
Blast gun |
one gun including boron cabide nozzle dia 8mm |
Squirt gun |
1 pc, dia 2mm. |
Air source |
5-7bar(kg/cm
2), 0.8-1.2m
3/min
|
Optional turntable |
---- |
dia 500mm manual |
dia 600mm manual |
dia 800mm maunal or electric 750W |
Optional |
1. Work car manual or powered & track assembly 2. Turntable manual or electric powered 3. Pneumatic vertical lift door 4. Adjustable gun mount 5. Multiple guns 5. oscillating systems |
|
Automatic Roller Conveyer Sand Blast Machine |
Automatic Roller Conveyor sand Blasting Machines are specially Developed for processing of long and flat steel sheets, glass sheet. The Sheets are ontinuously passing through the basting Chamber on a special roller Conveyor. Automatic Roller Conveyor sand Blasting Machines consist of a big cabinet enclosure, oscillating system, Multiple automatic suction blast guns, 2 automatic blow-off guns, cyclone reclaimers, reverse pulse cartridge dust-collector, roller conveyer system and control system, etc. Multiple blast automatic guns are fixed on the blast cabinet swinging over or moving horizontally over the sheet to produce a smooth, a sericeous surface, a bright shine appearance or to engrave on the surface of glass sheet. Large working chamber allows more options for gun placement and more room for maintenance..
|
Multiple blast automatic guns are fixed on the blast cabinet swinging over or moving horizontally over the sheet to produce a smooth, a sericeous surface, a bright shine appearance or to engrave on the surface of glass sheet. Large working chamber allows more options for gun placement and more room for maintenance.. Features: ▲. Adopt suction blast system. ▲. Continuously blasting. ▲. Multiple guns swinging or moving horizontally to cover whole top surface. ▲. Adaptability for different size (46#-80#) of nonmetal media to meet different process needs ▲. Roller Conveyers to move parts through the blasting cabinet. ▲. Reverse pulse cartridge dusct colleter |
|
|
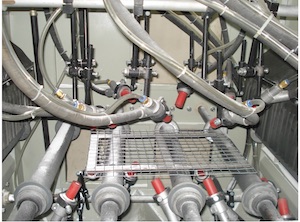 |
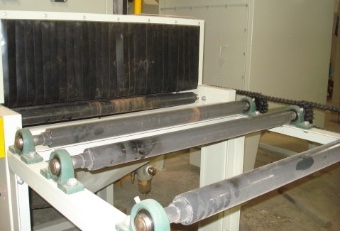 |
|
|
Model |
1211-12AR |
1520-4AR |
1823-8AR |
Processable components,mm, max, |
650WxT 250mm |
W1260mmx0.5-22mm |
L4mxW1.5mxT0.5-20mm |
Roller conveyor speed, m/min, With VFD |
0-5 |
0.2-0.8 |
0.2-0.9 |
Dimension, m, L x W x H |
5.4 x 1.3 x 3.5 |
8.1 x 2.0 x 3.61 |
10 x 4.3 x 4.25 |
Main cabinet, m, L x W x H |
3.4 x 1.3 x 2.13 |
1.5 x 2.0 x 2.01 |
1.8 x 2.3 x 2.31 |
Working chamber, m, L x W x H |
1.2 x 1.1 x 0.99 |
1.5 x 2.0 x 1.0 |
1.74 x 2.24 x 1 |
Conveyor frame, m, L x W x H |
1.0 x 1.1 0.99 |
3.0 x 2.0 x 0.96 |
4.1 x 1.9 x 1.16 x 2 |
Blast gun, pc |
12 |
4 |
8 |
Nozzle diameter, mm |
8 |
14 |
14 |
Light and control, Kw |
0.2 |
0.25 |
0.25 |
Dust collector, mm, Kw |
5.5 |
5.5 |
7.5 |
Conveyor, Kw |
0.75 |
0.75 |
1.5 |
Gun moving, Kw |
0.75 |
0.4 |
1.3 |
Blow-off, Kw |
0.75 |
0.75 |
0.75 |
Required compressed air |
12CBM@7 bar |
8CBM@7bar |
24CBM@ 7bar |
Option |
Elevator. |
Pressurized blast system |
Vibrating screen |
|
|
|
Pressure Blast Cabinets |
Pressure blast cabinet consists of cabinet enclosure, cyclone reclaimer & blast system and dust collector for tough cleaning, peening, deburring jobs. Compared to suction blasting, pressure blasting delivers higher abrasive media velocity for greater impact intensity, and can increase production rate by as much as 300 percent. |
It's widely used for process the surface of the forged parts, casting parts, welding parts, components after heat treatment, etc. |
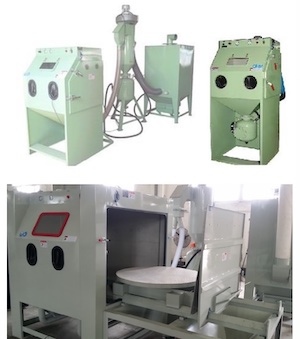 |
Features: 1. 24" long rubber gloves resist wear and protect operator. 2. Dst-proof light for extraordinary visibility. 3. Safety interlocks interrupt blasting if the door is opened. 4. Steel plate welded construction, with properly formed bends, forms a rigid, long-lasting cabinet shell. 5. Glass view window, exchangeable. 6. Pressure regulator, gauge, and electric switch mounted within easy reach. 7. One pressure blast gun with boron carbide nozzle dia 8mm. 8. Pneumatic foot pedal switch for activating blasting. 9. Built-in blow-off gun helps keep dust inside the cabinet. 10. Dry filter dust collecting, manually dust cleaning 11. Air source requirement: Pressure 8bar(kg/cm2); Flow 1.5-2m3/min. |
|
Model |
Cabinet (W*D*H mm) |
Work chamber (W*D*H mm) |
Motor (KW) |
Options |
8070P |
800*700*1800 |
800*700*580 |
1.1 |
1. Front door or/and side door 2. Manual turntable or Automatic turntable 3. Work car manual or powered & track assembly 4. Reverse pulse cartridge dust collectors 5. Pneumatic vertical lift door 6. Adjustable gun mount 7. P -type cabinets use nonmetal abrasive. 8. P-B Cabinets use metal abrasive without cyclone reclaimer |
8070P-B |
800*700*2400 |
800*700*580 |
0.37 |
9080P |
900*800*1800 |
900*800*580 |
2.2 |
9080P-B |
900*800*2400 |
900*800*580 |
0.37 |
10101P |
1000*1000*1910 |
1000*1000*1140 |
2.2 |
1010P-B |
1000*1000*2500 |
1000*1000*1140 |
0.55 |
1212P |
1200*1200*1900 |
1200*1200*950 |
2.2 |
1212P-B |
1000*1000*2600 |
1200*1200*950 |
0.55 |
1313P |
1300*1300*1900 |
1300*1300*950 |
2.2 |
1414P |
1400*1400*1900 |
1400*1400*950 |
2.2 |
1414P-B |
1400*1400*2600 |
1400*1400*950 |
0.75 |
1515P |
1500*1500*1900 |
1500*1500*950 |
2.2 |
1515P-B |
1500*1500*2600 |
1500*1500*950 |
0.75 |
|
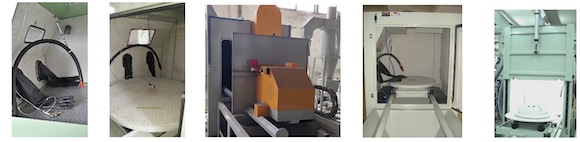 |
Suction Blast Cabinets |
Suction blast cabinets consist of cabinet enclosure, cyclone reclaimer and dust-collector, deliver efficient, affordable blast media to clean, peen, debur, or finish metal parts, easy use, low maintenance. Blast cabinet enclose the blasting environment to provide efficient blast cleaning while maintaining a clean surrounding work area. |
Features: 1. 24" long rubber gloves resist wear and protect operator. 2. Dust-proof light for extraordinary visibility. 3. Safety interlocks interrupt blasting if the door is opened. 4. Steel plate welded construction. 5. Large glass view window, exchangeable. 6. Pressure regulator, gauge, and electric switch mounted within easy reach. 7. One Suction blast gun with boron carbide nozzle dia 8mm. 8. Dry filter dust collector. 9.Manually dust Cleaning, 10. Built-in blow-off gun helps keep dust inside the cabinet. 11. Pneumatic foot pedal switch for activating blasting. 12. Compressed air source:5-7 bar, 0.8-1.2 m3/min |
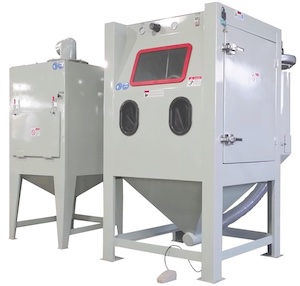 |
Model No. |
Dimension (W x D X H mm) |
Blast chamber (W x D X H mm) |
Side door opening (W x H mm) |
Window (W x H mm) |
Power (W) |
6050A |
600 x 925 x 1600 |
570 x 430 x 560 |
550 x 250 Front door |
250x 110 |
250 |
9060A |
900 x 960 x 1730 |
850 x 575 x 580 |
450 x 480 |
500 x 300 |
370 |
9080A |
900 x 1225 x 1800 |
870 x 730 x 650 |
500 x 450 |
500 x 300 |
370 |
1010A |
1000 x 1325 x 1900 |
950 x 950 x 850 |
800 x 900 |
500 x 300 |
550 |
1212A |
1200 x 1535 x 1900 |
1150 x 1150 x 850 |
950 x 900 |
500 x 300 |
750 |
1313A |
1300 x 1635 x 1900 |
1250 x 1250 x 850 |
1050 x 900 |
500 x 300 |
750 |
1414A |
1400 x 1735 x 1900 |
1350 x 1350 x 8500 |
1150 x 900 |
500x300 |
750 |
1515A |
1500 x 1835 x 1900 |
1450 x 1450 x 850 |
1250 x 900 |
500 x 300 |
750 |
|
Options: 1. Front door or/and side door 2. Heat device for fine abrasive mesh 180-320 3. Manual turntable 4. Swing manual turntable 5. Automatic turntable 6. Work car manual or powered & track assembly 7. Reverse pulse cartridge dust collectors 8. Pneumatic vertical lift door 9. Adjustable gun moun |
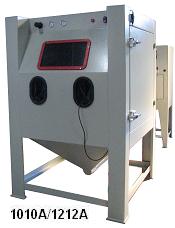 |
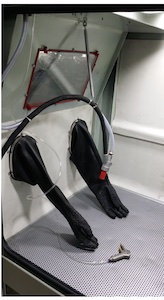 |
Multistation Blast Cabinets |
Multi-station sand blasting machines can in suction blast machine or in pressure blast machine, have big working cabinet and 2 to 6 operation station and 2-6 blasting guns for 2-6 operators to do blasting work simultaneously, can provide easy access to blast from either station for large, long and complex parts. Product Feature: 1. Long rubber gloves resist wear and protect operator. 2. Dust-proof lamp for better visibility. 3. Safety interlocks interrupt blasting if the door is opened. 4. Steel plate welded construction, with properly formed bends, forms a rigid, long-lasting cabinet shell. 5. Two to four stations provide easy access to blast from either station to accomodate long or complex parts. One nozzle and foot pedal are standard. 6. Large glass view window, exchangeable. 7. Pressure regulator, gauge, and electric switch mounted within easy reach. 8. Built-in blow-off gun helps keep dust inside the cabinet. 9. foot pedal switch for activating blasting. 10. Dry filter dust collector, manually dust cleaning. 11. Compressed air source requirement: :5-7 bar, 0.8-1.2 m3/min each blasting gun. |
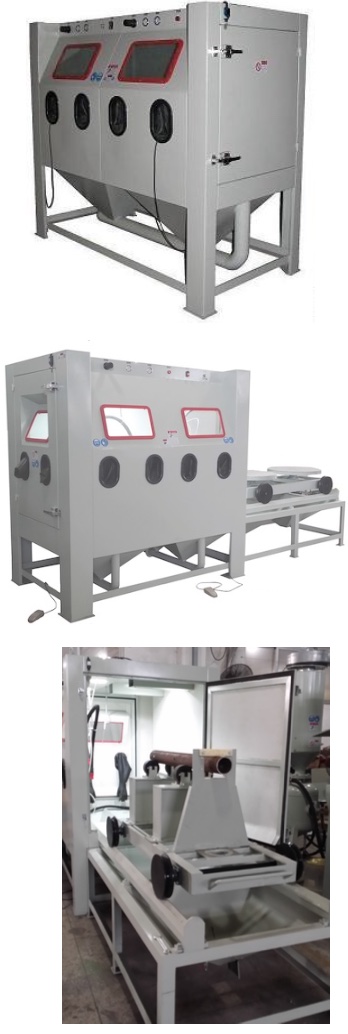 |
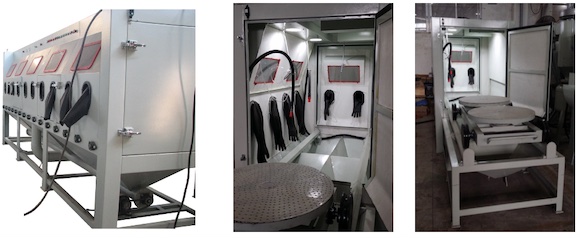 |
Model No. |
Cabinet (W x D X H mm)
|
Blast chamber (W x D X H mm)
|
Power
(W)
|
1012A2 |
1000 x 1200 1810
|
950 x 1150 x 850
|
1.1
|
2613A2 |
2600 x 1300 x 1810 |
2550 x 1150 x 850 |
1.1 |
2014A4 |
2000 x 1000 x 1810
|
1950 x 950 x 850
|
2.2
|
3015A6 |
3000 x 1500 x 1810
|
2950 x 1450 x 850
|
2.2
|
Option |
1. suction blast system
2. pressure blast syste
3. Manual turntable
4. Automatic turntable
5. Work car manual or powered & track assembly
6. Letf and right door, or front and back door
7. Reverse pulse cartridge dust collector.
8. Pneumatic vertical lift door
9. Adjustable gun mount
|
|
|
Automatic Belt Conveyer Blast Machines |
Automatic belt conveyer blast machines consist of cabinet enclosure, oscillating system, multiple automatic suction blast guns, one blow-off gun, cyclone reclaimer, cartridge filter dust-collector, belt conveyer system and control system, etc. It's suitable for automatic precise repeatable blast processing surface of small size components with or without complex profiles with no part-on-part contact possible, application ranges from delicate deburring to shot peening for small to middle scale production. The components are continuously passing through the blasting chamber, and the cleaning chamber on a special belt conveyor. Large working chamber allows more options for gun placement and more room for maintenance. Multiple automatic blast guns are fixed inside the cabinet make it possible to blast the components on all sides except of bottom. |
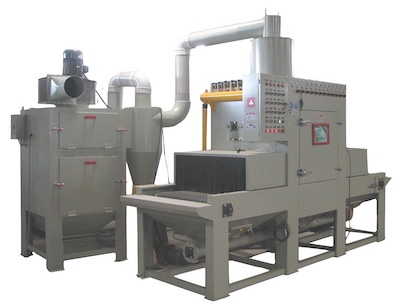 |
 |
Features:
- Capability to blast all sides of part simultaneously except for bottom Sturdy, mild steel blast cabinet for reduced maintenance and long life Single and multiple nozzle manipulation to direct media stream at specific part locations
- Adaptability for different size (80#-120#) of nonmetal media to meet different process needs
- Belt Conveyers to move parts through the cabinet
- Adjustable cyclone reclaimer for handling blasting media to reduce media consumption.
- Integral ventilation and dust collection.
|
|
Model |
1211-12 |
1085-6 |
1213-18 |
Processable Components,mm |
L1200*W550*H200 |
L400*W300*H200 |
W600XH200 |
Process capability m/min |
0.2~2.0 |
0.8~1.5 |
0.2~2.0 |
Dimension, (L x W x H), mm |
3400*1100*2510 |
2600*1600*2410 |
3400*1300*2020 |
Working chamber, (L x W x H),mm |
1200*1100*700 |
1000*850*750 |
1200*1300*820 |
Blast gun, with boron carbide nozzle |
12 pc, |
6 pc, |
12 pc |
Exhauster motor, KW |
3.0 |
3.0 |
5.5 |
Light and control,KW |
0.2 |
0.2 |
0.25 |
Conveyer motor,KW |
0.75 |
0.2 |
0.75 |
Oscillating motor,KW |
0.75 |
0.4 |
1.5 |
Screw motor,KW |
0.75 |
--- |
0.75 |
Reverse pulse cartridge dust collector |
4 cartridge filters |
4 cartridge filters |
6 cartridge filters |
Elevator motor, KW |
— |
— |
1.5KW |
|
|
Blasting Gun Air Consumption, nozzle dia 8mm
|
Cmrpessed air pressure (bar)
|
2.8
|
4.2
|
5.6
|
7.0
|
Cmrpessed air consumption of each gun (m
3/min)
|
0.51
|
0.70
|
0.88
|
1.07
|
|
|
|
Granet Recycling Machine |
Garnet Recycling Systems is used to reclaim and separate granular material. Main function is to remove all coarse contaminations like nails, nuts, stones, welding rod ends, cigarette butts, broken glass, wood, extract dust to get reusable material.
The system consists of inlet port, bucket elevator, screw conveyor, air separator, vibratory screen,sand hopper, cartridge filter dust collector with automatic reverse pulse dust cleaning, and electrical control system etc.
|
The contaminated abrasive garnet is loaded into the feed port, and then it is picked up by the bucket of the elevator and raised up by elevator and dropped into the inlet chute to the rotating screen.
The internal screw of the rotary screen remove the large contaminates to the end for disposal. Particles small than 4.8mm fall through the rotary screen mesh and form a curtain, falling onto the vibrating screen.
Air current generated by the built in dust collector are introduced to create a simple air wash. Bu adjusting the air flow, the amount of the undersized material or fines removed can be controlled. The dusty air is then drawn to the dust collector and the fines drop into the disposal container.
The garnet then falls through the vibratory screen. The particles small than 0.7mm will pass through this screen, and collected in the hopper below and can be emptied into a bulk bag or drum.
|
|
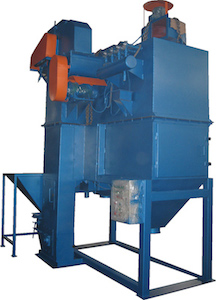 |
|
Dust collector has 4 Cartridge, 12 square meter filter area per cartridge. Reverse pulse cartridge dust collectors allow non-stop, high-production. The cartridges are automatically pulse cleaned for maximum filter efficiency.
Specification:
Model: |
RS5.0 |
Capacity: |
5000kg/hour max (put-through) |
Elevator motor: |
2.2kw |
Screw conveyor motor: |
2.2kw |
Dust exhauster motor: |
3.0kw. |
Dimension: |
3000mm(W)x2600mm(L)x3700mm(H) |
Required compressed air: |
0.9m3/min, 0.6Mpa. |
|
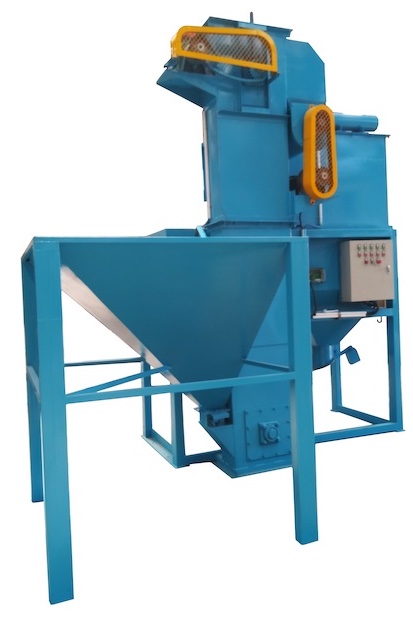 |
|
Stainless Steel Shots are widely used for deburring and brightening of the surface of aluminium alloy, zinc alloy, colorful metal and stainless steel, etc. They are of austenite structure with execellent features of high strengh and tough, low consumption, none dust, quick clean speed and good clean results. They can extend fatigue life, enhance corrosion- resisting and brighten the surface of parts. The hardness for new material state is appro 300HV, for usage state is about 450HV. Its specific gravity is 7.8g/cm3 and bulk density is 4.7g/cm3. Physical & Chemical Specification. C =0.15-0.20% Si=1.5-2.5% Mn=0.9-1.2% Ni=7.0-10.0% Cr=16-20% Other Remark: Hardness: Before Use HV-250 After Use HV-450
Product Specification/Models S10: 0.05-0.2 mm S20: 0.1-0.3 mm S30: 0.14-0.5 mm S40: 0.4-0.8 mm S50: 0.6-1.0 mm S60: 0.7-1.25 mm S100: 1.00-1.40 mm S150: 1.25-1.7 mm S200: 1.4-2.0 mm S300: 1.7-3.0 mm
Overhead rail spin hanger(s) shot blasting machine are specially suitable for the treatment of sensitive parts, particularly complex, heavy, or large metal castings or forging parts without part-on-part contact possible. The parts are mounted on a hook and transported into the blasting chamber. Multiply highly efficient blast wheels fixed on the machine housing make it possible to treat the components on all sides. The rotating of the hanger(s) ensure that the blasting media, accelerated by the blast wheels, reache every component, providing the best possible uniform blasting result.
Straight rail or Y rail shot blast machines
|
Model
|
RHSB376
|
RHSB378B
|
RHSB378C
|
RHSB378E
|
Processable parts,mm, max
|
φ600× 1100
|
φ800× 1500
|
φ900× 1500
|
φ900× 1500
|
Hanger load capacity, kg
|
600
|
1000
|
1000
|
1000
|
Blast wheel, kg/min
|
2×120
|
2×180
|
2×250
|
2×250
|
Ventilationm3/h
|
5000
|
7200
|
8300
|
8300
|
Power, kw
|
19
|
28
|
37.4 |
39.65
|
|
Model
|
RHSB3710
|
RHSB3720
|
RHSB3730
|
RHSB3750
|
Processable parts,mm
|
φ1200× 1800
|
φ1400× 2200
|
φ1600× 2300
|
φ1800× 2500
|
Hanger load capacity, kg
|
1000
|
2000
|
3000
|
5000
|
Blast wheel, kg/min
|
2×250
|
3×250
|
3×250
|
4×250
|
Ventilationm3/h
|
9000
|
15000
|
15000
|
18000
|
Power, kw
|
39.65
|
61.27
|
64.4
|
78.4
|
|
Rotary Drum Shot Blast Machines |
Rotary drum Shot Blasting Machine specially designed for economic and consistent treatment of small to mid-sized iron, steel, alloy and non-ferrous castings, forgings, heat treated parts, pressings and Fabrications components, which are small, flat and light and normally unsuitable for processing in tumble belt shot blast machines at the lowest possible cost.
|
|
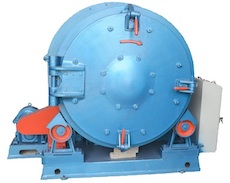 |
|
Specifications |
|
Model |
3110 |
3110B |
1 |
Drum Diameter |
1000mm |
2 |
Drum Length |
800mm |
3 |
Drum speed |
3.0 rpm |
4 |
Drum Effective Volume |
100L max |
5 |
Loading capacity |
300kg max |
6 |
Processable component length |
400mm max |
7 |
Processable single component weight |
15kg max |
8 |
Production capacity |
600-1500kg/h |
9 |
Cleaning period |
Iron castings |
3-10 min |
Steel castings |
10-20 min |
forgings |
4-8 min |
10 |
Drum |
Motor |
1.1kw |
Speed |
48rpm |
11 |
Disc Bucket Elevator |
Quantity |
16 |
Capacity |
0.4L |
12 |
Blast wheel |
Motor |
7.5kw, 1450rpm |
Rotary |
2300rpm |
Diameter |
427mm |
Width |
62mm |
Blast capacity |
100kg/min |
Speed |
60m/s |
Direction |
Clockwise |
Blast area |
60°~70° |
Blast width |
100-200mm |
13 |
Abrasive |
Dia. |
0.8-1.2mm |
14 |
Abrasive consumption |
Iron castings |
5-10kg/T |
Steel castings |
10-20kg/T |
forgings |
8-15kg/T |
15 |
Dust collector |
Cyclone separator |
Dry filter |
Ventilation volume, m3/h, approx. |
800 |
2000 |
Separate efficiency |
85% |
99% |
Separate motor |
1.1kw, 2825rpm |
2.2kw, 2900rpm |
Dust Cleaning |
-- |
0.37kw, 1400rpm |
16 |
Total power |
9.7KW |
11.17kw |
17 |
Dimension, mm |
2078*2458*1861 |
3400x2458x3370 |
18 |
weight |
3575kg |
4100kg |
|
high quality Zinc cut wire, aluminium cut wire, stainless steel cut wire and copper cut wire from China at competitive price and excellent service. Zinc cut wire, Aluminium cut wire and aluminium cut wire are widely used for shot peening to give compressive residual stress in the surface layer of components for fatigue life enhancement and suppression of stress corrosion cracking and deburring and cleaning of zinc or aluminum die cast parts without any damage to the parts, and creating much less dust than natural and artificial corundum abrasives. Available sizes: Zinc Cut Wire: 0.8mm, 1.0mm, 1.2mm, 1.5mm, 1.8mm, 2.0mm, 2.5mm Conditioned Zinc Cut Wire: 0.6mm, 0.7mm, 0.8mm, 1.0mm, 1.5mm, 2.0mm, 2.5mm Aluminium Cut Wire:0.6mm, 0.7mm, 0.8mm, 1.0mm, 1.5mm, 2.0mm, 2.5mm Copper Cut Wire:0.6mm, 0.8mm, 1.0mm, 1.5mm, 2.0mm, 2.5mm Stainless Steel Cut Wire is widely used for shot peening to give compressive residual stress in the surface layer of components for fatigue life enhancement and suppression of stress corrosion cracking as well as cleaning and polishing of the surface of metal parts, deburring of die cast parts, is of reusable and recyclable, the working life is 1000 times of glass bead. Stainless steel cut wire can produce very bright surface, but creat much less dust than glass beads, natural and artificial corundum abrasives. The hardness is 20-40HRC. Available sizes: 0.2, 0.3, 0.4, 0.5, 0.6, 0.8, 1.0, 1.2, 1.5, 2.0, 2.5mm. If you are interested in this item, please feel free to contact us.
|
|
|
|
|
|